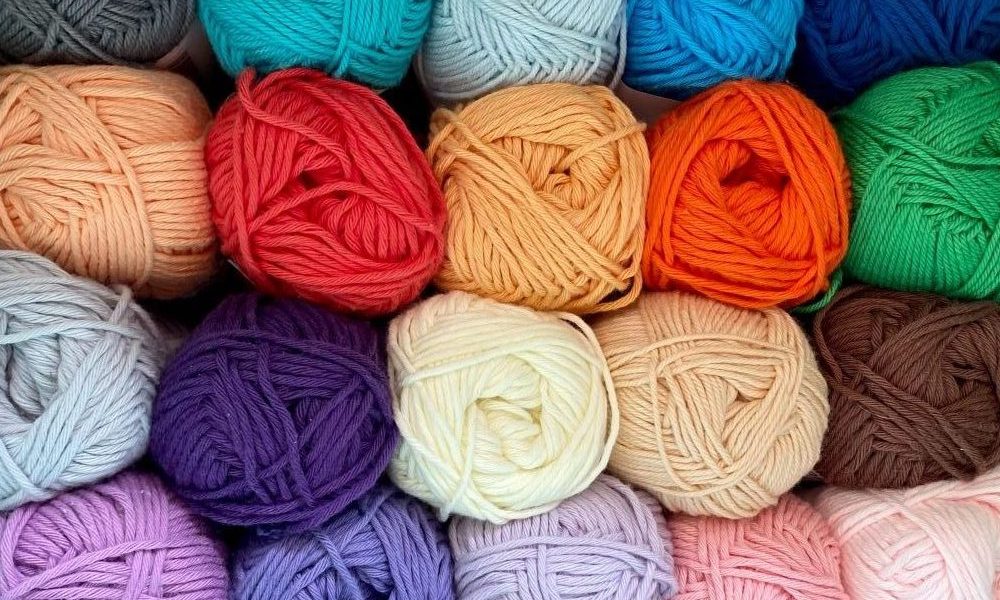
Britain, Sheep, and wool – part 1
Article by Sean Wilkinson – Nordstar Director of international markets – Nordstar is Datatex UK Business Partner
BRITAIN, SHEEP, AND WOOL
Sheep, one of our greatest natural resources, one of Britain’s greatest natural resources. Sheep have grazed in Britain for thousands of years and, although in the last 50 years both sheep farming and the wool textile industry in the Britain have shrunk considerably, their strong roots remain.
Fossilised remains suggest that wild sheep evolved between 10 and 20 million years ago in the mountains of Central Asia. Coloured black, brown or grey to provide camouflage, they would have had a hairy outer coat and a softer, woolly undercoat, all of which would have moulted in the spring. It is not clear how these early wild sheep migrated to Asia, Europe, and North Africa or when they were domesticated. Nevertheless, it is known that primitive people tamed wild sheep for food and clothing and went on to learn to spin and weave. It is likely that some selection of breeding stock took place to produce whiter wool rather than dark hairy fibres, a theory supported by the legend of the Golden Fleece, amongst other historic references.
Sheep were on the move, spreading through Egypt, North Africa, and then Europe. The Romans became skilled sheep breeders and their influence spread alongside their empire. In Britain, although pelts may have been worn as early as 3000 BC, the early Bronze Age, spinning, and weaving are thought to have developed during the late Bronze Age, around 1900BC. The native sheep at that time were descended from a small, long-legged breed, developed from the wild sheep of Northern Europe. The Britons had already established a wool industry when the Romans invaded in 55 BC. They brought with them sheep that were larger with finer, white wool. They established a wool plant in what is now Winchester, England as early as 50 AD. The time was ripe for further industrial development. By the 3rd century hard wearing British Wool, said to be ‘spun so fine that it is in a manner comparable to the spider’s web’, was a major export, much of it to Italy. The Romans left their imported sheep to breed with native British flocks and when, later, the Vikings arrived they too brought their own breeds of black-faced, horned sheep, ancestors of some of today’s well-established breeds in Britain.
By the 12th century, raw wool was abundant and wool cloth making was widespread from which considerable revenue was made from the exports of both. During this period, wool became the backbone and driving force of the English economy. Interestingly, the largest flocks of sheep were in the hands of the abbeys and monasteries, yet Henry VIII would later upset that status quo.
The consistently high quality of English wools from the Cotswolds and Lincolnshire and Welsh wools from central Wales, the Welsh marches, meant that they were in great demand by foreign, woollen textile manufacturers. Hence, from the late thirteenth to the late fifteenth centuries, there was a boom in English raw wool exports to Flanders and Italy, which were Europe’s major producers of high-quality woollen textiles and its most advanced industrial regions. But by the late 14th century, successive taxes levied on the wool industry to fund the wars with France had, unintentionally, forced England to develop its own handwoven cloth market. Rather than send wool abroad to be woven into cloth, which was then bought back at greatly inflated prices, wool merchants and entrepreneurs realized they could make their own and sell it both domestically and abroad. This burgeoning cloth industry was given a further boost by an influx of skilled Flemish cloth weavers invited by Edward III in the 14th century in the hope they could show English crafters how it was really done.
By the 16th century, England is largely a nation of sheep farmers and wool textile manufacturers, and it was around the 1550s when England’s “Empire of Wool” was established, when wool and wool textiles accounted for 90% of England’s exports. These exports were destined to a single city, Antwerp. Unfinished woollen broadcloths manufactured in Gloucester, Wiltshire, and Somerset (these were dyed and finished in Antwerp to suit the central European market), finished broadcloths produced in Kent left London for Antwerp. So too would Kersey cloth (made with Kersey yarn from Kersey, a town in Suffolk), a lighter and cheaper cloth than broadcloths, used in the production of military uniforms, and manufactured, dyed, and finished in Yorkshire. These Kersey cloths would leave for Antwerp through the ports of Hull and Newcastle. From Antwerp, these English wool textiles would then travel overland to Italy.
However, change was on the horizon. The Dutch Revolt in the Low Countries during the 1560s-80s brought to an end the dominance of Antwerp as a trading hub. As a consequence, thousands of skilled Flemish and Dutch clothmakers fled to England to avoid religious persecution, settling in the Cotswolds, the West Country, Yorkshire, Kent and East Anglia. They once more brought with them techniques for making much lighter wool cloths than those generally produced by the English, the so-called “new draperies” (worsteds, named after the village of Worstead in Norfolk), which found a ready market in the much warmer Mediterranean climes than the traditional, heavy woollen broadcloths produced for warmth.
In 1454, Parliament had declared that ‘the making of cloth within all parts of the realm is the greatest occupation and living of the poor commons of this land’. Monarchs passed numerous laws to prop up the English woollen cloth market and compel its subjects to wear home-grown textiles. The Cappers Act of 1571 stated that most people must wear, on Sundays and holidays, a ‘cap of wool, thicked and dressed in England […] upon pain of forfeit for every day not wearing 3s 4d’. In 1697 it was decreed that all magistrates, judges, undergraduates, and law professors had to wear woollen gowns. Only a few years earlier, various Burial in Wool Acts, made between 1666 and 1680, stated that every person must be buried in an English woollen shroud, unless the deceased had been destitute or had died as a result of the plague. It was decreed that: ‘no corps should be buried in anything other than what is made of sheep’s wool only; or put into any coffin lined or faced with any material but sheep’s wool, on pain of forfeiture of £5’.
So, the English worsted industry was established and grew, helped by a vibrant home demand and, during the seventeenth century, an overseas trade that outstripped its Dutch rivals to capture new Mediterranean markets as the Italian and Spanish textile industries went into decline. In the 1660s, wool and wool textile exports still represented two-thirds of England’s foreign commerce and East Anglia, the West Country, and the West Riding of Yorkshire became centres for the British wool textile industry.
This galloping demand for English wool cloth was satisfied by independent workers, and their families who plied their craft at home, sometimes to supplement farming. Women spun yarn (spinsters), often helped by children. The yarn then went to a weaver, usually a man, who might be another family member weaving cloth for the household. It is more than likely, both spinsters and weavers were working in the “putting out” production system. Cloth merchants supplied the wool in its various states to a wide network of home-based out-workers, who would then transform the fibre into yarn, or the yarn into semi-finished fabric, or the semi-finished fabric into finished fabric. Some out-workers, spun, others wove, dyed or finished. The cloth merchants would then travel round, delivering and / or collecting raw materials, semi-finished or finished cloths and, either pass them onto the next out-worker in the supply chain or take the finished cloth to one of the many cloth halls (A cloth hall contained trading stalls for the sale, particularly, of cloth but also of leather, wax, salt, and exotic imports such as silks and spices.) across the country. The system may have been domestic (piecework) but the scale of trade was enormous, and was reflected in the grand architecture of the many cloth halls. The Piece Hall in Halifax, built between 1775 and 1779, is a prime example.
Halifax became well known for producing Kersey cloth. The town also had another claim to fame. The Halifax Gibbet was the only guillotine type of apparatus in England. Installed during the 16th century, it was used to execute petty thieves on market days, especially those who stole woollen cloth. It was later abolished in the 17th century during Oliver Cromwell’s reign.
A lack of representation by any form of guild or labour union left outworkers especially vulnerable. As with all piecework carried out at home, the control lay ultimately with the merchant who didn’t have to bear the cost of renting the premises and / or machinery, training, or heating. Wool workers made up the largest manufacturing sector in the British economy by the middle of the 18th century. Out of a population of 6 million, a quarter worked in wool textiles.
This well-established production system, however, was going to undergo a huge revolution. An Industrial Revolution.
The British damp climate is ideal for grazing sheep, so for centuries, Britain was renowned for its fine woollens. Flax, the raw material for linen, also thrives in rain. Linen and wool were used to make the linsey-woolsey worn by all but the richest people in the Middle Ages and Renaissance. Silk, introduced by French Protestant silk workers fleeing persecution in the 17th century, was also made in Britain, mostly in London.
Fine woollens aside, wool production was difficult to mechanize because centuries-old laws protected traditional ways of making it. Conversely, by the 1740s silk was already being machine-made in factories in Derby and Macclesfield with equipment based on pirated Italian designs. But silk was too delicate and expensive for mass consumption. Cotton, on the other hand, was hardwearing, comfortable, and inexpensive. Unlike wool, its production was not controlled by ancient practices because it had only become widely available after the East India Company began exporting it from India in the late 17th century. Inventors, therefore, bent their minds to creating cotton-processing machines, and cotton spearheaded the British industry into the textile mill (factory) system. 18th century machines typically used waterpower, hence the siting of early textile mills near the fast-flowing rivers of the Pennines. By the middle of the 19th century, Britain was producing half the world’s cotton cloth, and yet not a scrap of cotton was grown in Britain. Textile mills were popping up everywhere.
The locations in which these textile mills popped up, however, were often remote and the locally available workforce insufficient in number. The solution to this lack of a workforce was a little disturbing, however. Demanding entrepreneurs, backed by government, were encouraged to recruit the most vulnerable people in society, orphans and destitute children from the age of five, and turn them into what have been dubbed the ‘white slaves of England’. Many didn’t know what they were going to do, often duped with promises of a life of fresh air, plentiful of food, and an education. In return for meagre food and board, children were expected to work fourteen to seventeen hours a day, six days a week, until they reached the age of twenty-one. Employing children made financial sense. Factory owners and overseers didn’t want to employ adults who demanded higher wages and less regimented ways of working. Children could be moulded and coerced. Not only that, but many of the machines were deliberately designed to be operated by young children, with their tiny hands, slight bodies, and quick reflexes. The factory act of 1833 banned children under nine from working in the textile industry and limited the hours of those aged between nine and thirteen. Nearly thirty years after the Factory Act, half of all of England’s children between the ages of five and fifteen were classed as ‘working’.
This first Industrial Revolution (1760-1840) brought enormous change. It’s almost impossible to imagine the pace of change that this revolution induced into the woollen industry during the 19th century. At the start of the century, there were around 250,000 hand-loom weavers across Britain. By 1850 this number had fallen to 40,000, and by 1860, only 3,000 remained.
When textile mill technology moved from away from waterpower to steam power, it transformed coal mining into a major industry. Serendipitously, England’s richest mines were also near the Pennines in Lancashire, Yorkshire, Nottinghamshire, and Derbyshire. Thus, these northern areas became the textile strongholds of the country. Wherever coal was plentiful, textile mills would spring up close by and workers would flood to them in their thousands. The machines that clattered in textile mills boosted the iron industry. The demand for quick, efficient methods of bringing raw materials to the textile mills and taking away the finished cloth stimulated first the canal system and then the growth of the railways.
The arrival of cotton, the advent of the textile mill, and the birth and growth of the American textile industry not only changed the woollen textile industry, but they also changed the British landscape, the industrial landscape, a way of life, forever.
REFERENCES
- American Wool ‘The History of Wool Fact Sheet’;
- ‘A Short History of the World According to Sheep’ by Sally Coulthard;
- British Wool ‘British Sheep & Wool’;
- Business of Fashion, Textiles, and Technology (BFTT) ‘Mapping the UK Fashion, Textiles and Technology Ecosystem’;
- IWTO ‘Market Information No. 17’;
- UKFT ‘Compendium of Industry Statistics and Analysis 2020’;
- The Alliance Project and NBrown – National Textiles Growth Programme May 2017 ‘Realising the growth potential of UK Fashion and Textile Manufacturing’.