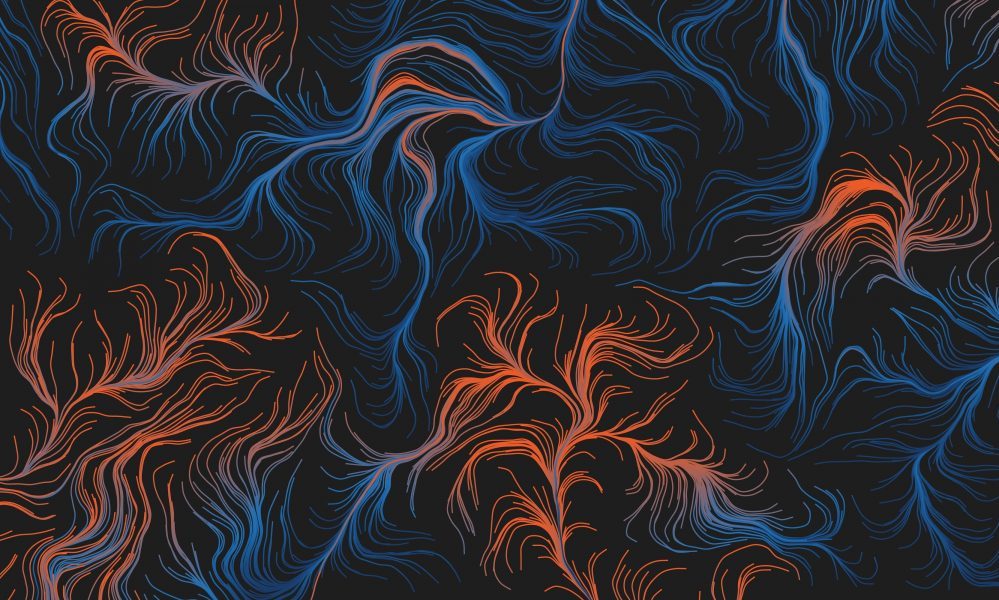
Energy crisis. The impact on Italian textile companies
Interview with Ferdinando Botto Poala – CEO Botto Giuseppe e Figli S.p.a
BOTTO GIUSEPPE E FIGLI S.P.A. – A historic Italian textile company founded in 1876, Botto Giuseppe is headquartered in Valdilana, in the province of Biella, and produces fabrics, jerseys, yarns for knitwear, needlework, weaving and accessories. It has a turnover of more than 60 million euros and about 300 employees, and also operates through its factory in Tarcento, Friuli Venezia Giulia.
The bills for electricity and gas that have been coming in recent months to Italian textile companies present – compared to a year ago – increases that reach in some cases up to +800% and that – in the “luckiest” cases in any case we see doubled or tripled numbers compared to the same period last year. What impacts does this energy shock – linked to Russia’s war in Ukraine and the difficult international geopolitical situation – have, in the immediate term, on Made in Italy textile production? How can companies respond?
Energy costs, which had already increased significantly in the last months of 2021 and the beginning of 2022, are now – a year later – literally spiraling out of control, and not only quantitatively. The situation is difficult because the bills are much higher – certainly – but also because one is forced to work in a situation of absolute uncertainty, in which it is practically impossible to plan and schedule what will be on the one hand the orders and on the other hand the costs to be incurred (and therefore the quotations to be established and proposed to customers). We are navigating by sight in a context in which not even we can be certain of having the gas we need for next year, assuming that even more alarming war scenarios do not open up – even for us – given the dramatic evolution that the conflict between Russia and Ukraine is having. Hoping that from the point of view of war there will be no further degeneration, it still remains open – for Italian textile companies – the problem of getting through unscathed what is to all intents and purposes a perfect storm, which sees a concomitance between the post-Covid increase in demand, the non-programmability of work (in a world like ours that was once used to operating within a framework of seasonality with easily predictable times of inertia), the difficulty in finding skilled and motivated staff (partly because during the Covid years quite a few people working in the textile-fashion industry moved on to other sectors), and finally the energy shock and thus the increase and extreme volatility of electricity and gas costs.
It used to be said in the textile world that in order to be competitive, an Italian company ideally had to have a labor cost of less than 20 percent of turnover, otherwise it would have a strong incentive to relocate. Today the cost of labor, in Italian textiles, can fall even to lower levels, and in this respect we have become competitive. However, it is clear that if gas and energy costs increase five or six times, it becomes very difficult to compete with textile companies from countries outside Europe (for example, Turkey, China, India or Pakistan) that have not had such increases.
How can Italian textile companies react?
Focusing on product quality and – from the energy point of view – reducing consumption and increasing self-production of renewable and sustainable energy, something we have been doing for over twenty years (since 2001) with major investments. Reducing waste and adopting an eco-sustainable approach, in the textile world, is now no longer just an ethical choice, or an advantage in terms of communication and marketing, but in the future perspective it also becomes an essential element to be competitive in terms of production costs. At this stage there are those who would like to turn back on the ecological front, adopting a short-term view in the face of an emergency. That would be a very serious mistake. We must understand that only by incentivizing the clean energy self-production of Italian companies, and only if we overcome the excesses of the textile-fashion system (sales-waste-sales-etc.) can we have a future, acquiring solidity and autonomy with respect to changing international economic and geopolitical conditions.
To what extent is this energy shock likely to result, in the short and medium term, in a halting of the reshoring process from Asia -which had received a strong boost from the pandemic and the global supply chain crisis- and a further shift of Italian textile production to Turkey and other non-European production centers?
Over the past two years, there has been a crisis in global supply chains that has led to an unprecedented increase in the cost of intercontinental transportation and logistics services, with extreme elements of uncertainty and delivery delays that have brought to the forefront the issue of reshoring textile production in Italy and Europe. If containers leaving Asia cost ten times more than they did three years ago, and if it is not known with certainty either when or if they will arrive at their destination, it is clear that a major opportunity opens up for companies producing in Europe, a momentous opportunity that this energy crisis is completely thwarting. If Italian and European institutions manage to intervene adequately to deal with the energy emergency, interesting scenarios may open up – on the issue of reshoring textile production, otherwise the outlook could quickly become dramatic. On the issue of gas and electricity in Italy we are tightening the noose around our necks, and someone – at the political level – must intervene quickly to stop this suicide.
Italy, operating within a European framework, is moving to achieve greater energy self-sufficiency within a few years. In the immediate term, however, textile companies need concrete and rapid support. As a textile entrepreneur and manager, what do you ask of Italian and European institutions? What policy interventions do you hope for?
A beneficial effect of the pandemic (one of the few…) was the increase in the pro-European sensibility of the governments and populations of the various European countries, and this new sense of European unity boded well with respect to the evolution of a continent that if it really wants to count for something in the face of the American and Chinese empires must be united and cohesive. Unfortunately, once the critical phase of the pandemic emergency has passed, divisions and partisan approaches have returned, with the Northern European countries that-having long since dismantled and relocated what little manufacturing they had, and having considerable average wealth-are underestimating the impact of the energy shock on European industrial production, and on the other hand the countries with a strong manufacturing vocation such as Italy that lack the capacity and political clout to make their demands in the EU. The first thing I hope as a textile entrepreneur is that Europe – in the face of the energy crisis – will come back together and that the northern European countries will understand that supporting the European manufacturing fabric is a choice that also provides them with greater security for the future, in a context of extreme uncertainty and globalization gone mad and constantly evolving like the one we are going through and with which we will continue to have to deal in the coming decades. We need an EU limit on the price of gas and electricity, a price that must become stable again, it must allow companies to plan year after year for production as they used to do, without this extreme uncertainty that prevents any industrial planning at the moment, and it must allow citizens to cope without family drama with paying their bills.
The second thing I hope for as an entrepreneur is more seriousness on the part of the Italian institutions and political class, with respect to the problems of business and in relation to the ecological transition, which is the core from which to address the energy crisis for the future as well. In recent years I have seen in Italy too many extemporaneous bonuses thrown around haphazardly and subject to abuses of all kinds, too many subsidies, too many election commercials, too many public companies-in the field of renewable energy-that have served more to spin money and armchairs than to adequately address the problems, too much bureaucracy and too many abstruse rules that have disincentivized companies and citizens from really investing on this front. Reducing energy dependence is a strategic goal for Italy, but it is achieved through a serious approach, not through chaotic, haphazard, and misguided initiatives.
How is your company doing – at this difficult time – to cope with the energy crisis?
We are moving as we have always done over the past two decades, that is, investing in renewable energy, photovoltaics and energy self-production.
On this front, we have moved well in advance of the current energy crisis, with investments that have involved-in our Valdilana (Biella) factory-cogeneration plants, air conditioning systems, compressors, pumping stations and burners, lighting, heat recovery from condensate re-evaporation the installation of recuperators on boiler smokestacks, the recovery and reuse of cooling water from compressors, the installation of continuous combustion control on steam generators, and the installation of a microturbine that takes advantage of the hydraulic jump between the industrial water intake work located 70 meters above the plant and the storage tanks serving the departments. While at our factory in Tarcento, Friuli, we have intervened by modernizing the hydroelectric power plant serving the plant, installing photovoltaic panels on the roofs of the plant, improving air conditioning systems, containing compressed air leaks, installing LED lamps, replacing the old boiler with a new condensing boiler, installing a turbine that recovers discharged water to maintain minimum vital runoff on the Torre stream, and even trying to create a vegetable oil power plant.
ITA
Crisi energetica. L’impatto sulle aziende tessili italiane
Intervista a Ferdinando Botto Poala – CEO Botto Giuseppe e Figli S.p.a
BOTTO GIUSEPPE E FIGLI S.P.A. – Storica azienda tessile italiana fondata nel 1876, Botto Giuseppe ha sede centrale a Valdilana, in provincia di Biella, e produce tessuti, jersey, filati per maglieria, aguglieria, tessitura e accessori. Ha un fatturato di oltre 60 milioni di euro e circa 300 dipendenti, e opera anche attraverso lo stabilimento di Tarcento, in Friuli Venezia Giulia.
Le bollette per l’energia elettrica e il gas che stanno arrivando in questi ultimi mesi nelle aziende tessili italiane presentano – rispetto a un anno fa – aumenti che arrivano in certi casi fino a un +800% e che – nei casi più “fortunati” – mettono capo comunque a numeri raddoppiati o triplicati rispetto allo stesso periodo dell’anno scorso. Questo shock energetico – legato alla guerra della Russia in Ucraina e alla difficile situazione geopolitica internazionale – che impatto sta avendo, nell’immediato, sulla produzione tessile Made in Italy? Come possono reagire le aziende?
I costi energetici, che erano già aumentati sensibilmente negli ultimi mesi del 2021 e all’inizio del 2022, ora – a distanza di un anno – stanno andando letteralmente fuori controllo, e non soltanto dal punto di vista quantitativo. La situazione è difficile perché le bollette sono molto più alte – certamente – ma anche perché si è costretti a lavorare in una situazione di incertezza assoluta, nella quale è praticamente impossibile pianificare e programmare quelli che saranno da una parte gli ordini e dall’altra i costi da sostenere (e quindi le quotazioni da stabilire e proporre ai clienti). Si naviga a vista in un contesto nel quale nemmeno possiamo avere la certezza di avere il gas necessario per il prossimo anno, sempre che non si aprano – anche per noi – scenari di guerra ancora più allarmanti, data la drammatica evoluzione che sta avendo il conflitto tra Russia e Ucraina. Sperando che dal punto di vista bellico non ci siano ulteriori degenerazioni, resta comunque aperto – per le aziende tessili italiane – il problema di attraversare indenni quella che è tutti gli effetti una tempesta perfetta, che vede una concomitanza tra l’aumento post-Covid della domanda, la non pianificabilità del lavoro (in un mondo come il nostro che una volta era abituato a operare in un quadro di stagionalità, con tempi di inerzia facilmente prevedibili), la difficoltà nel trovare personale competente e motivato (anche perché negli anni del Covid non poche persone che lavoravano nell’ambito del tessile-moda si sono spostate su altri settori), e infine lo shock energetico e quindi l’aumento e l’estrema volatilità dei costi dell’energia elettrica e del gas.
Un tempo si diceva, nel mondo tessile, che per essere competitiva un’azienda italiana doveva avere idealmente un costo della manodopera inferiore al 20% del fatturato, altrimenti avrebbe avuto una forte convenienza a delocalizzare. Oggi il costo della manodopera, nel tessile italiano, può scendere anche a livelli inferiori, e sotto questo aspetto siamo diventati competitivi. È chiaro però che se i costi del gas e dell’energia aumentano di cinque o sei volte, diventa molto difficile competere con le aziende tessili di Paesi extraeuropei (per esempio Turchia, Cina, India o Pakistan) che non hanno avuto aumenti di questo tipo.
Come possono reagire le aziende tessili italiane? Puntando sulla qualità del prodotto e – dal punto di vista energetico – riducendo i consumi e incrementando l’autoproduzione di energia rinnovabile e sostenibile, cosa che noi facciamo da oltre vent’anni (dal 2001) con importanti investimenti. Ridurre gli sprechi e adottare un approccio ecosostenibile, nel mondo tessile, ormai non è più soltanto una scelta etica, o un vantaggio in termini di comunicazione e di marketing, ma in prospettiva futura diventa anche un elemento imprescindibile per essere competitivi sul piano dei costi di produzione. In questa fase c’è chi vorrebbe tornare indietro sul fronte dell’ecologia, adottando un’ottica di breve periodo di fronte a un’emergenza. Sarebbe un errore gravissimo. Dobbiamo capire che solo incentivando l’autoproduzione energetica pulita delle aziende italiane, e soltanto se superiamo gli eccessi del sistema del tessile-moda (saldi-sprechi-invenduto-ecc.) possiamo avere un futuro, acquisendo solidità e autonomia rispetto alle mutevoli condizioni economiche e geopolitiche internazionali.
In che misura questo shock energetico rischia di determinare, sul breve e medio termine, un blocco del processo di reshoring dall’Asia – che aveva ricevuto una forte spinta dalla pandemia e dalla crisi delle supply chain globali – e un ulteriore spostamento delle produzioni tessili italiane in Turchia e in altri centri di produzione extraeuropei?
Negli ultimi due anni c’è stata una crisi delle supply chain globali che ha portato a un incremento inedito nei costi dei trasporti e dei servizi logistici intercontinentali, con elementi di incertezza estremi e con ritardi nelle consegne che hanno portato in primo piano il tema del reshoring delle produzioni tessili in Italia e in Europa. Se i container che partono dall’Asia costano dieci volte di più rispetto a tre anni fa e se non si sa con certezza né quando né se arriveranno a destinazione, è chiaro che si apre un’opportunità importante per le aziende che producono in Europa, un’opportunità epocale che questa crisi energetica sta vanificando completamente. Se le istituzioni italiane ed europee riescono a intervenire adeguatamente per fronteggiare l’emergenza energetica si possono aprire – sulla questione del reshoring delle produzioni tessili – degli scenari interessanti, altrimenti le prospettive potrebbero diventare rapidamente drammatiche. Sulla questione del gas e dell’energia elettrica in Italia ci stiamo stringendo il cappio intorno al collo e qualcuno – a livello politico – deve intervenire rapidamente per bloccare questo suicidio.
L’Italia, operando in un quadro europeo, si sta muovendo per raggiungere, nel giro di alcuni anni, una maggiore autosufficienza energetica. Nell’immediato, tuttavia, le aziende tessili hanno bisogno di un sostegno concreto e rapido. Da imprenditore e manager tessile cosa chiede alle istituzioni italiane ed europee? Quali interventi politici auspica?
Un effetto benefico della pandemia (uno dei pochi…) è stato l’aumento della sensibilità europeista dei governi e delle popolazioni dei diversi Paesi europei, e questo nuovo senso di unità europea faceva ben sperare rispetto all’evoluzione di un continente che se vuole contare davvero qualcosa di fronte agli imperi americano e cinese deve essere unito e coeso. Purtroppo, superata la fase critica dell’emergenza pandemica, sono tornate le divisioni e gli approcci di parte, con i Paesi del Nord Europa che – avendo smantellato e delocalizzato da tempo la poca manifattura che avevano, e avendo una ricchezza media considerevole – stanno sottovalutando l’impatto dello shock energetico sulla produzione industriale europea, e dall’altra i Paesi a forte vocazione manifatturiera come l’Italia che non hanno la capacità e il peso politico per far valere le proprie istanze in sede Ue. La prima cosa che auspico come imprenditore tessile è che l’Europa – di fronte alla crisi energetica – torni a compattarsi e che i Paesi nordeuropei capiscano che sostenere il tessuto manifatturiero europeo è una scelta che garantisce anche a loro una maggiore sicurezza per il futuro, in un contesto di estrema incertezza e di globalizzazione impazzita e in continua evoluzione come quello che stiamo attraversando e con il quale continueremo ad avere a che fare nei prossimi decenni. Serve un tetto Ue al prezzo del gas e dell’elettricità, prezzo che deve tornare stabile, deve consentire alle aziende di pianificare anno su anno la produzione come si faceva una volta, senza questa incertezza estrema che impedisce al momento qualsiasi programmazione industriale, e deve consentire ai cittadini di far fronte senza drammi familiari al pagamento delle bollette.
La seconda cosa che come imprenditore auspico è una maggior serietà delle istituzioni e della classe politica italiana, rispetto alle problematiche delle imprese e in relazione alla transizione ecologica, che è il fulcro a partire dal quale affrontare per il futuro anche la crisi energetica. Negli ultimi anni ho visto in Italia troppi bonus estemporanei lanciati a caso e soggetti ad abusi di ogni genere, troppi sussidi, troppi spot elettorali, troppe società pubbliche – nell’ambito delle energie rinnovabili – che sono servite più a far girare soldi e poltrone che ad affrontare adeguatamente i problemi, troppa burocrazia e troppe regole astruse che hanno disincentivato le aziende e i cittadini a investire veramente su questo fronte. La riduzione della dipendenza energetica è un obiettivo strategico per l’Italia, ma la si raggiunge con un approccio serio, non con iniziative caotiche, disordinate e sbagliate.
La sua azienda come si sta muovendo – in questo momento difficile – per fronteggiare la crisi energetica?
Ci stiamo muovendo come abbiamo sempre fatto negli ultimi vent’anni, cioè investendo nelle energie rinnovabili, nel fotovoltaico e nell’autoproduzione energetica.
Su questo fronte ci siamo mossi con largo anticipo rispetto alla crisi energetica attuale, con investimenti che hanno riguardato – nella nostre fabbrica di Valdilana (Biella) – gli impianti di cogenerazione, gli impianti di condizionamento, i compressori, le centrali di pompaggio e i bruciatori, l’illuminazione, il recupero termico dalla rievaporazione condense, l’installazione di recuperatori sui camini delle caldaie, il recupero e il riutilizzo dell’acqua di raffreddamento dei compressori, l’installazione del controllo in continuo della combustione sui generatori di vapore, l’installazione di una microturbina che sfrutta il salto idraulico tra l’opera di presa acqua industriale posta a 70 metri al di sopra dello stabilimento e le vasche di accumulo a servizio dei reparti. Mentre nella nostra fabbrica di Tarcento, in Friuli, siamo intervenuti ammodernando la centrale idroelettrica a servizio dello stabilimento, installando dei pannelli fotovoltaici sui tetti dello stabilimento, migliorando gli impianti di condizionamento, contenendo le perdite di aria compressa, installando lampade a Led, sostituendo la vecchia caldaia con una nuova caldaia a condensazione, installando una turbina che recupera l’acqua scaricata per mantenere il deflusso minimo vitale sul torrente Torre, e provando perfino a creare una centrale ad olio vegetale.