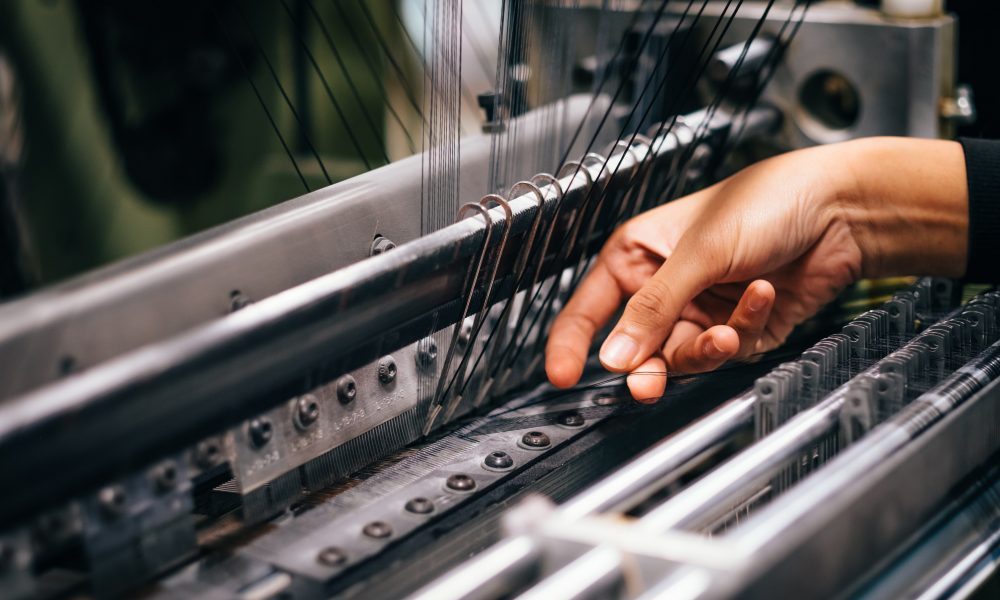
Industry 4.0 and its effects on the Textile Sector
Article written by CLAUDIO BALLOTTA – Datatex Sales and Marketing Manager Americas
When we read Industry 4.0, the first thing we think about is the Fourth Industrial Revolution. This might come as a surprise, not a long time ago we found articles talking about the third industrial revolution and now there are some specialists going even further and announcing the fifth or sixth industrial revolutions.
Without willing to generate further confusion with the topic, the idea of this article is to reflect on the previous industrial revolutions, make a comparison with our current situation and in a very general way, review the effect it is having on the textile and clothing industry.
Analyzing the past, the first thing we noticed is that industrial revolutions were transitional processes that took several years. The first ones took a long time and the recent ones, not so much. These were not linear transformations, where a discovery changed the way people work overnight. They were complex transitions, with many discoveries and several versions of inventions, some successful and others not. The most successful inventions were accompanied by changes that transformed the economy, production process, work and even the way people live.
Interestingly, the first industrial revolution is closely related to the textile industry. In fact, it was the dominant industry and was the first to use modern production methods. In 1764, James Hargreaves invented “Spinning Jenny”, a machine that could spin several spindles at once. In 1784 (twenty years later), Edmund Cartwright developed the first loom powered by a steam engine, considered the most representative invention of this period.
Some inventions found applications completely different from those initially thought of by their creators. For example, James Watt invented the steam engine to pump water out of coal mines. Later, this technology was applied on the locomotive and steamships. The steam engine allowed installations that were previously located near streams of water, used as power source to move wheels and mill stones. This represented a boost that was crucial for industrial development.
The First Industrial Revolution represented the passage of a society with an economy focused on agriculture and craftsmanship, to another based on industrial production and the development of cities. The Second Industrial Revolution used electrical energy to create mass production. The transformation into an industrial society was strengthened. Cities were transformed and continued to grow. New means of transportation appeared, such as cars, aircraft, and trains, as well as new communication technologies, like the telegraph and the phone.
The Third, which is more familiar to us, was based on electronics and the development of information and communications technologies to automate production and build an increasingly service-oriented economy.
The Fourth Industrial Revolution
One of the most accepted definitions comes from the World Economic Forum, precisely from its founder Klaus Schwab:
“The Fourth Industrial Revolution represents a fundamental change in the way we live, work and relate to one another. It is a new chapter in human development, enabled by extraordinary technology advances commensurate with those of the first, second and third industrial revolutions.”[i]
It considered that this was not an extension of the Third Industrial Revolution for three reasons:
- The speed of the changes, which has no historical precedents. For example, the phone took 50 years to reach 5 million users. The television took 22 years, and the Internet, 7 years to reach the same audience. Pokemon GO in just 19 days reached that same volume.
- The scope of the changes, which impacts almost all industries and countries.
- The breadth and depth of these changes, which heralds the transformation of complete production, management, and governance systems.
The next question is what technologies are driving these changes. In previous industrial revolutions, we could clearly identify which ones were most important in driving the changes. In Industry 4.0 it is not even one, it is a set of different technologies that are generating this transformation process.
An interesting approach developed by consulting firm McKinsey[i] suggests classifying these new technologies into four large groups:
- Data, Computational Power and Connectivity: In this group we find technologies such as Cloud Computing, Internet of Things (IOT), Big Data and Quantum Computing. They are related to data processing, integration, and storage capacity.
- Analytics and Artificial Intelligence: Technologies that deal with the collection, preparation, processing and use of data. Artificial intelligence is a field of great development with the dissemination of Machine Learning and Deep Learning techniques.
- Human-machine interaction: Augmented Reality, Virtual Reality, Exoskeletons and Ubiquitous Computing are some examples of the technologies of this group. It refers to new ways how humans can relate to all kinds of machines.
- Digital to physical conversion: This is how we apply in the physical world the choices we make after analyzing the information or model created in the digital world. Robotics is one of the main technologies in this group.
Next, we will review the applications we have found for each of these groups in the textile and clothing industry.
Data, computational power, and connectivity
As in many other industries, cloud computing generates a lot of interest and several companies are exploring its use while others have already adopted it for the interesting advantages it offers. The main one is to access IT resources quickly and flexibly without the need for large upfront investments.
For example, Datatex offers its ERP Textile NOW also in the cloud and many customers prefer this mode to avoid maintaining their own Data Center and delegate work related to the operation and updating of the system. This allows them to focus on activities directly related to their core business and turn information system management and update responsibilities into one more service that can be outsourced.
As for the Internet of Things (IoT), the reduction in sensors and actuators costs makes it possible to include them in all types of machines and equipment. This represents an improvement in the automation, configuration, and monitoring systems, which manufacturers now incorporate into their own equipment. At the last ITMA fair there was a large deployment of such applications in virtually all manufacturers.
This is a particularly important requirement for Industry 4.0, as information from each machine belonging to a work center or plant can be consolidated and monitored. Indeed, systems could be created that use this data to control the operation and plan the optimal sequence of tasks that must be performed to meet the demand plan and the commitments made with customers. This makes the concept of Digital Twins a reality, where a real physical system has a digital representation in a mathematical model that reflects its behavior. This allows you to not only control and decide on the physical system, but to do simulations and experiment with different scenarios to make better decisions. This concept can go beyond the confines of the same company and extend to the resources of the entire supply chain, seeking to produce and reach the final product to the customer in a fast and efficient way. A vision that different research centers are trying to make a reality in different types of industries.
Another key technology in this group is Big Data. This refers to a data set that is too large or complex for ordinary computing devices to process.
A huge Excel file with a lot of data is not Big Data, despite how large we can consider it to be. While the textile industry produces a large volume of data, we have not found companies that share success stories, at least in planning, production, or quality functions. The retail industry uses this type of technology to accumulate data that is used to prepare demand forecasts. In this case, the source is the data gathered from social networks or from the navigation of visitors to their websites. Textile companies with well-known brands may use these types of technologies. In general, the applications of this group’s technologies in the textile industry are like those we can find in any other industry.
Artificial Intelligence and Analytics
Artificial intelligence is the most relevant technology in this group. It is a broad concept, that includes areas such as Machine Learning and Deep Learning. It is important to correctly define these concepts.
Artificial intelligence refers to computer technology capable of performing tasks that normally require human intelligence, such as learning and problem solving. This includes several applications, from software capable of playing chess to things as sophisticated as a self-driving car.
Machine Learning is a subset of artificial intelligence. It is an application that can learn from the data, without having to be explicitly programmed. Machine learning algorithms create a model based on a set of samples, known as “training data”. The model thus developed will be able to make predictions or make decisions when new data arrives. For example, Netflix uses machine learning to generate models that recommend movies based on the user’s profile. Similar applications are used by Amazon, Spotify, YouTube to make recommendations that fit the preferences of each specific customer.
Deep Learning is a subset of Machine Learning. It uses algorithms inspired by the structure and function of the brain called artificial neural networks. This leads to a learning process that is much more sophisticated and versatile. It is used for voice recognition, natural language processing, computer vision (image recognition), chat-bots and autonomous vehicles.
In the case of the textile industry, most artificial intelligence applications are geared towards using computer vision and image recognition to replace or increase human observation and examination of textile samples – usually to detect errors and anomalies, detect defects during fabric inspection, and color matching.
In all these cases, the implementation requires a training phase where the data with which the system will be trained must be prepared, so that the system learns by itself to recognize and detect a correct sample and distinguish it from a faulty one. This involves preparing hundreds of images of good and bad samples. If it is fabric quality, we must have several examples for the different types of defects that may occur,as well as examples of fabrics without quality problems. Each sample must have the corresponding tag (good or wrong) for system training to occur. The larger the sample, the better prepared the system to detect quality problems. The system does is learn to distinguish flawed patterns from what they are not.
While there are some commercial offerings for this type of technology, it is still at an early stage and there are no customers who want to publish success stories for such applications. The textile engineering faculties of some universities have also experimented with these technologies. In these cases, applications are related to research and development activities, which even go towards new forms of use, such as:
- Virtual yarn modeling from fiber properties
- Automatically detect and measure wrinkles in fabric
- New fiber modeling methods
We can conclude that the application of Artificial Intelligence in the textile and clothing industry is just starting, and although there are some interesting use cases, there does not appear to be widespread adoption. In other sectors, such as banking, insurance, and retail, or in the automotive and electronics industry, applications are more mature, and the number of use cases and supplier offerings are significantly higher.
As other industries find more and more Artificial Intelligence applications to improve their business and operations, we can expect them to also spread to the textile industry in the coming years.
Human-machine interaction.
In this group we find Virtual Reality and Augmented Reality technologies, through mobile devices such as smartphones, tablets, holographic glasses, and lenses with virtual screens. There are also Voice Interaction, gesture interaction technologies, and extension devices such as exoskeletons.
The main driver of this group is a greater familiarity among consumers with new ways of interacting with machines, which comes from the increasing use of personal devices.
Touch interfaces are already ubiquitous in the consumer world and devices for voice and gesture commands, as well as virtual and augmented reality devices are increasingly in use. Similarly, these devices will increasingly begin to be used as a natural feature in work and production environments making human-machine interaction easier and more friendly.
When it comes to augmented reality, we find many applications for fashion retail, but not so much in textile production. There are cross-applications for guided maintenance or operator instructions through mobile devices or smart-glasses for virtual training, but this is nothing specific to the textile world.
Within this group we can also find electronic textiles or e-textiles. This addresses fibers with electronic functions to generate, transmit, modulate, and detect electrons and some external stimuli. Interactive textile electronic devices can provide suitable platforms for virtual reality and augmented reality applications due to their excellent performance and unique immersive features such as lightness, flexibility, comfort and low voltage even under high deformations. This is an innovation that could open new markets from these types of materials and their use in clothing and accessories.
Digital to Physical Conversion.
In this group, a combination of declining costs, expanding the range of materials and advances in accuracy and quality are the drivers of their growing importance. We find disruptive technologies such as additive manufacturing (or 3D printing) and robotics.
Additive Manufacturing or 3D printing has gone a long way from being only applicable to polymers and metals to a wide range of materials, including glass, biocells, sugar and cement. There are some 3D printing applications in the textile industry with flexible materials such as producing padding and soles for snickers and shoes and developing very innovative garments. While the garments produced with these materials are expensive and not as comfortable as a traditional garment, they stand out for their originality.
Robotics is an area that has been gaining a lot of relevance in the recent years due to significant advances in artificial intelligence, artificial vision and M2M (machine to machine) communication. The use of robots has a long history in some industries, such as in the automotive and electronics industries. In the textile industry we also find several interesting and very promising applications.
Leaving aside general-purpose robotics applications, such as those related to the transfer and handling of objects and boxes, there are applications for specialized tasks, such as pocket sewing, fabric laying and recently sewing robots. It is important to note that while the latter is a stand-alone application, the previous two are collaborative applications, where a human operator and the robot work in a coordinated manner.
Indeed, sewing robots have aroused a lot of interest as they promise to perform in a similar or better way than a human sewing line, including handling cut parts throughout the process. Applying video cameras, robotic arms and very precise displacement systems, these robots can produce garments with high levels of quality and productivity.
While we are in the early versions of such robots, we are likely to see a lot of activity in the coming years. This technology generates a lot of expectation in the industry and manufacturers of this type of equipment are experiencing high demand for this kind of robots.
In conclusion, we can see that of all the disruptive technologies that are at the base of Industry 4.0, there are few practical applications specific for the textile and clothing industry. On the other hand, we can say that several of the general applications, which are used by different types of business, are also leveraged by the textile industry, such as Cloud Computing and the Internet of Things. It is important to note that there are very promising applications, which are at an early stage of their life cycle and that have great potential to change the industry, such as robotics and artificial intelligence.
Unlike the first industrial revolution, where the textile sector was the most important, the impact of Industry 4.0 on the textile industry has not yet been as relevant as in other sectors. As we indicated at the beginning, these processes take time, and many innovations and technological advances are not static and are in a constant process of adaptation and innovation. We will most likely continue to see creative applications of these disruptive technologies and we must be very aware of their effects and ability to transform traditional business models.
Today more than ever, textile and clothing companies must be prepared not only to deal with a market that is becoming increasingly fast, competitive, and complex; but also, be able to assimilate and integrate with new technologies and adapt their processes. This implies an organizational culture open to change, agile and dynamic working processes, and a versatile information system that supports them and facilitates optimal and informed planning, execution and decision-making at all level.
[i] Industry 4.0 How to navigate digitization of the manufacturing industry. McKinsey & Company. 2015