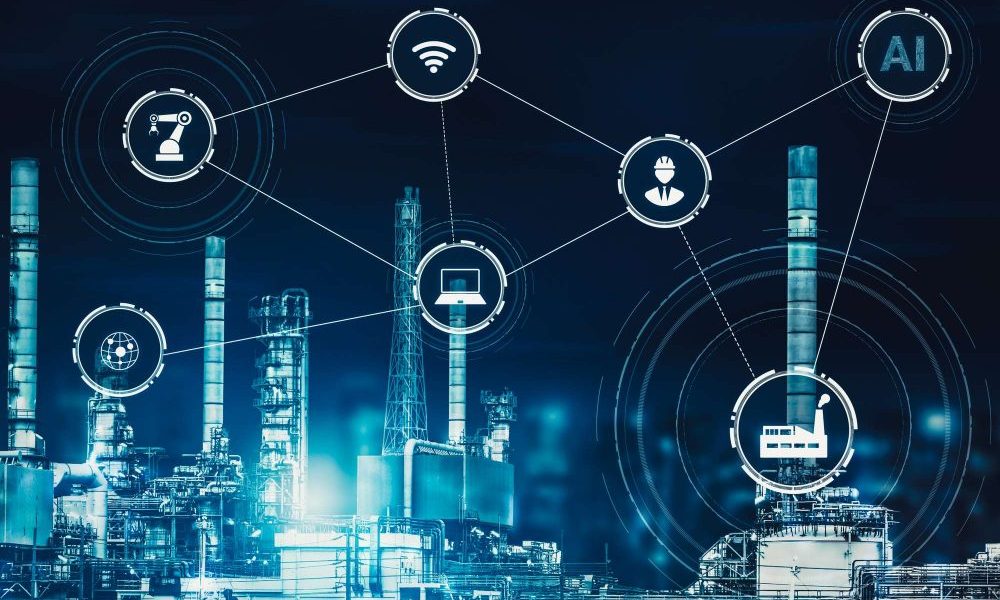
Textile Industry 4.0. Where do we stand?
Interview with Gaetano Tonello – Datatex Senior Project Manager
When people talk today about Industry 4.0 it is mostly done by referring to calls for tenders and funding, often without adequately clarifying the technical aspects of what is – or should be – a real ‘Fourth Industrial Revolution’, after the First (between the 1700s and 1800s, with the development of Watt’s steam engine and innovation in the textile and metal industries), the Second (between the 1800s and 1900s, with electricity, oil, the internal combustion engine, chemicals and mass production for mass markets) and the Third (in the second half of the 1900s, with information technology, computers and management software). Industry 4.0 means many things, including Artificial Intelligence, Machine Learning, Big Data, Internet of Things, Cloud and Smart production. Concretely, and looking specifically at the field of textile production, what can be the scope of this revolution and what could be the most innovative features from the point of view of – for example – quality control, production planning, Predictive Maintenance and production defect detection?
If we want to summarize the concept, Industry 4.0 introduces a new buzzword, that of ‘Smart Factory’, literally ‘Intelligent Factory’.
In recent times, due to the Covid-19 pandemic, we have heard a lot of talk – often in vain – about ‘Smart Working’, i.e. what ‘Smart Work’ should – and should have been; much less have we heard about ‘Smart Factory’.
The theorists of the new stage opening behind the curtain of Industry 4.0 point to ‘Cyber-physical Systems’ (i.e. ‘physical’ systems closely and inseparably connected to ‘IT’ systems) as the key to Industry 4.0, whereby the ‘Smart Factory’ becomes the fusion of ‘Smart Production’ (i.e. the ‘intelligent’ interaction between operators, machines and tools), ‘Smart Services’ (i.e. the ‘intelligent’ set of structures, IT and otherwise, that enable direct and unmediated communication between customers and suppliers, as well as between companies and external structures) and ‘Smart Energy’ (i.e. everything that in an ‘intelligent’ manner contributes to reducing energy consumption and likewise the environmental impact of industrial production).
So, when we talk about Industry 4.0, before we think of declining everything into the realm of Artificial Intelligence, we need to be aware of this fundamental assumption, namely that it is good that everything should be as ‘intelligent’ as possible, but not necessarily ‘artificial’.
It has been about twelve years since anyone started talking about the ‘Fourth Industrial Revolution’, and in this period we have to all intents and purposes entered the ‘era of variability’, where the acceleration of technological progress and the continuous mutability – not to say volatility – of knowledge in many disciplinary fields impose the need to think and elaborate continuously new strategies, under conditions of ever-increasing complexity and unpredictability.
In this context around us, the game is likely to be played on two fields:
In the Smart Factory, processes and products must not only make use of, but also ‘incorporate’, ‘process’, ‘metabolize’ and ‘improve’ pre-coded information, while at the same time constantly interacting with many variables in the operating environment, exchanging information with the ‘key players’ involved, whether they are other producers and/or other consumers and/or other users. And this is the field in which ‘Artificial Intelligence’ plays.
In the Smart Factory, communication skills – as they say in the slang – become in fact the most important part of the operators’ skills and professionalism: we are in the presence of overcoming the traditional conception of ‘individual task’ and ‘professional competence’, because what each person does is embedded in a set of information flows that can change relentlessly: those who stop at what is ‘known’ and what is ‘certain’ risk being left behind.
But between saying and doing… lies the sea…?
Let us just think for a moment about how people still work – and produce – in many of the textile/manufacturing companies known to us, and try to ask ourselves some questions.
- Is the work and skill set of the ‘human resource’ focused on doing basically ‘smart’ things?
- Isn’t time (and thus ‘value’) wasted doing things that are repetitive, sometimes redundant or otherwise related to a scenario that is absolutely predictable and controllable by an algorithm?
- Are the computer processes set up to direct, control and analyze physical processes just something random – they ‘run’ for those interested in them, who make sure they ‘run’ them just enough when they are needed – or are they the ones that make machinery run ‘efficiently’, ‘effectively’ and ‘economically’, enabling human resources to do ‘intelligent’, i.e. inherently much more useful things?
- Is ‘corporate information’ – which is the company’s most important intangible asset – something ‘unique’ and ‘univocal’ (collected and catalogued in a single form, with a single method, at a precise moment, by a single person or a single system and made available to all in the same form, substance and usability) or is it something scattered in a thousand different places, at the mercy of the initiative of individuals and the ‘interpretative goodwill’ of those who want and/or need to make use of it?
If the answers to these questions are what I think they are, then we can agree that Industry 4.0 can make sense, indeed it makes sense and is not just a slogan.
Concretely.
I am reminded of a scenario at EOS Textile Ltd. (Savar, Bangladesh), where the fully automated interaction between our NOW™ System and Automha S.p.A.’s automated warehouse not only optimizes the loading and unloading flows of all materials and finished products, but also eliminates any errors due to miscommunication or misinterpretation of what and how much should be ‘loaded into’ or ‘taken out of’ the warehouse.
And also in the EOS, thanks to the constant and total interaction between NOW™ and the Antara™ loom control system by INCAS S.p.A., warping and weaving production is programmed on all machines and kept constantly under control, thus making it possible to plan well in advance the subsequent processing phases, as well as to have the evolution of each single piece of fabric produced in real time under one’s eyes.
Or Flash SRB doo (Apatin, Serbia), a company in which all the systems for managing the fabric dyeing department are interconnected to NOW™, namely the management of the dyeing laboratory of Intex System S.r.l., the volumetric dosing machine of SALCE S.r.l, the control of the dyeing machines of Orgatex Setex Gmbh, the “colour kitchen” of Datacolor; here, all systems speak the same language: a single article code, a single colour code, a single combination of recipe and colour, a single “Production Order” valid for communicating to all systems what is to be sampled or produced, and collecting from the systems what has been produced, in what quantity, at what time and consuming what dyes and auxiliary materials.
Or the Stamperia di Martinengo S.r.l. (Martinengo, Italy) where everything that is carried out in some of the printing, steaming, washing and finishing machines is fed back into NOW™ in real time, and where NOW™ – by maintaining an ‘inferential engine’ of data received from the machines – is in turn able to ‘suggest’ to the machines what is the appropriate steaming and/or washing recipe for each item to be processed, or what is the correct cylinder setup of the printing machine for a given design. In this case, a bit of A.I., which doesn’t hurt…
There are many more such examples – taken at random by our customers – ranging from relatively minimal, but controlled and error-proof situations (collection of machine control data with handheld terminals, by means of bar code readings) to rather ‘pushy’ situations (functions on the ERP system that directly control the PLCs of the machines, flanking or ‘fully’ replacing the action of the operator).
However, it would be a mistake to make the assumption that Industry 4.0 is merely a matter of ‘enabling technologies’: what is most important in studying and fine-tuning what is the ‘Enterprise Information Management System’ is that everything must contribute to producing – and selling – more and better, wasting less.
Any transition phase is also historically accompanied by communicative and rhetorical aspects that emphasise elements that are instead destined to only minimally affect concrete change in the industry. In textile 4.0, which aspects are, in your opinion, over-emphasised and over-emphasised in terms of their possible impact?
I would say that in order to adequately answer this question, we first need to clear the field of a potential misunderstanding: when thinking about the ‘Smart Service’ component of Industry 4.0, it can be misleading to reason generically in terms of ‘IT inculcation’ as a natural continuation of ‘IT literacy’.
Let me explain.
We come from decades of computer ‘literacy’; by now, in almost all the textile/manufacturing companies that we have known over the years and helped to grow and improve, the various Information Systems that make up what is known as the ‘Company Information Management System’ already in many cases exchange data without anyone doing – or thinking – anything; already a large part of the operators working on the machinery no longer use paper, pen and inkwell to note down what they have done or to record the data collected and communicate them to those who have to use or analyze them; the normal relationship between the company and its customers is no longer hinged on e-mails, but on real ‘portals’.
Consequently, in the current context, the widespread tendency that has ‘historically’ taken hold is that in the context of Industry 4.0 investments, the company should simply take a small step forward and ‘computerize’ a little more.
Unfortunately, this process of ‘inculturation’ was – and still is – seen almost as a ‘necessary evil’.
In Italy, the legislator, well aware of the potential negative consequences of what has just been stated, behind the wording ‘Industry 4.0’ promulgated in December 2016 a law on what were called the ‘incentives for the technological and digital transformation of companies’, incentives that were reiterated year after year, and are still in force today.
On the one hand, these incentives have tickled the ‘lucrative’ imagination, leading to the proliferation of IT projects that are not very ‘smart’, not to say ‘fake’; on the other hand, they have created overly emphatic and unrealistically reliable expectations: not a few entrepreneurs have dreamed of being able to halve their workforce by investing – not too much, for goodness’ sake – in the ‘ultimate IT project’…
Industry 4.0 is not a slogan; it means believing that – by investing seriously – we can seriously improve.
Do you see potential dangers – from a human and ethical point of view – in an exaggerated and radical 4.0 approach? How can the Artificial Intelligence revolution be handled wisely, forward-looking and balanced?
It is very recent news that Google Artificial Intelligence researcher Blake Lemoine has been placed on administrative leave (= fired) after publicly stating that “…LaMda, a language model designed to converse with people, it was sentient…”.
At one point, according to reports in the Washington Post, Lemoine even went so far as to request that LaMda be represented by a lawyer, adding that his belief in the ‘personality’ of the language model was based on the fact that LaMda had told him that he had a soul.
The possibility of more ‘intelligent’ A.I. applications gaining awareness is a topic that has been addressed often, especially in the face of attempts by companies such as Google, Microsoft, IBM and Nvidia to ‘train’ large-scale language models in recent years.
Personally, I think that the problem we face today is on a distinctly different plan, and that – as usual – we go out of our way to ‘distract’ public opinion – the ‘common people’ – and take it to another ideal side.
The concept of Industry 4.0 has no direct connection with the concept of Artificial Intelligence.
There is only ‘mixing’ between the two.
Artificial Intelligence today is – and can be – exclusively functional for Industry 4.0.
Not vice versa.
Or rather, Industry 4.0 cannot and should never be subservient to Artificial Intelligence.
In the evolution of things, however, I see only one – great – risk, and that is the one, which unfortunately has already occurred for example in the banking and financial sector – that A.I. will be perceived by ‘insiders’ as something capable of replacing the ‘person’ at the heart of everyday decision-making.
This possibility in the textile/manufacturing world must absolutely not occur.
The textile/manufacturing world has overcome so many crises in the last 25 years, because there is no artificial intelligence that holds: there is the ‘natural’ intelligence of people, of human resources.
Artificial Intelligence comes later, and helps to do things better.
In layman’s terms, Industry 4.0 can and should be a great help, it can and should allow one to make ‘the big leap’, but it can never replace the person.
Datatex is today the international leader in ERP solutions for the textile industry, and has always sought to be a partner for industries in the sector seeking innovation and change. How can Datatex help textile companies with regard to Transition 4.0?
Well, let’s start by saying that several companies we have already helped, and continue to help, day after day.
Beyond this, our philosophy of life – our ‘company name’ – does not change, and what we propose to our Partners – to call them ‘Customers’ nowadays is a bit reductive – is constantly evolving in concrete terms according to the evolution of technologies, but conceptually it has not changed over time, it will never change, and can be summarized as follows: fewer steps, fewer people directly involved, less chance of error, more alternatives allowed, more exceptions managed, more flexibility in the interpretation of a situation, of a condition, wider margins of action in decision-making processes, narrower margins in repetitive processes, less time lost in triggering and controlling something attributable to an algorithm, more time spent thinking about and verifying what an algorithm can never judge on its merits.